Quels indicateurs pour mesurer la performance de vos machines ?

Pour atteindre les objectifs d’une démarche Lean ciblée sur la performance des machines, il est nécessaire d’exploiter toutes les données liées aux performances et la disponibilité des machines.
Nous allons donc aborder dans cet article une sélection d’indicateurs à utiliser pour une analyse pertinente de la productivité de vos machines.
Les indicateurs de suivi de la maintenance
Les machines doivent être surveillées de près pour que les services de maintenance sachent quand intervenir et qu’ils sachent quelles seraient les conséquences d’une réparation en termes de perte de temps et donc de productivité.
La performance des opérations de maintenance joue un grand rôle dans la productivité globale d’une entreprise, nous aborderons dans cette partie une sélection d’indicateurs qui permettront de mesurer cette performance.
- MTBF – Mean Time Between Failure = Temps Moyen Entre Pannes
Exprimer en nombre d’heures, le Mean Time Between Failure – MTBF (Temps Moyen entre pannes) est un indicateur qui permet de déterminer si un équipement est fiable.
Il peut être déterminant dans le choix de remplacement d’un équipement s’il est jugé trop court et entraîne des arrêts à répétition causant des pertes de performance de productivité conséquentes.
MTBF = Temps de Fonctionnement Brut / Nombre de Pannes
- MTTR : Mean Time To Repair = Temps Moyen de Réparation
Le MTTR permet de savoir combien de temps est nécessaire, en moyenne, pour détecter et localiser une panne et remplacer la pièce défectueuse, il peut mettre en évidence la nécessité de trouver des solutions pour rendre les opérations de maintenance plus simples et plus rapides.
MTTR = Temps de Panne / Nombre de Pannes
Indicateurs suivi performance machine
Voici une sélection d’indicateur à utiliser pour une analyse pertinente de la productivité de vos machines.
- Taux de Rendement Synthétique – TRS
Il exprime l’aptitude de l’entreprise à utiliser au meilleur de leurs performances les équipements mis à disposition sur la base du temps pendant lequel ces équipements sont donnés à la production pour les utiliser.
Il peut savoir comment les équipements ont fonctionné selon 3 critères :
- La disponibilité
- Leurs performances
- La qualité
Le calcul du TRS
Le TRS se décompose en 3 taux :
Le taux de disponibilité – Do : Il représente le pourcentage du temps d’ouverture pendant lequel les équipements sont prêt à travailler.
Le taux de performance – Tp : Il représente le pourcentage du temps brut de fonctionnement où la production est faite à la cadence prévue.
Le taux de qualité – Tq : Il représente le pourcentage du temps net de fonctionnement passé à faire des pièces bonnes.
TRS = Tq * Tp * Do
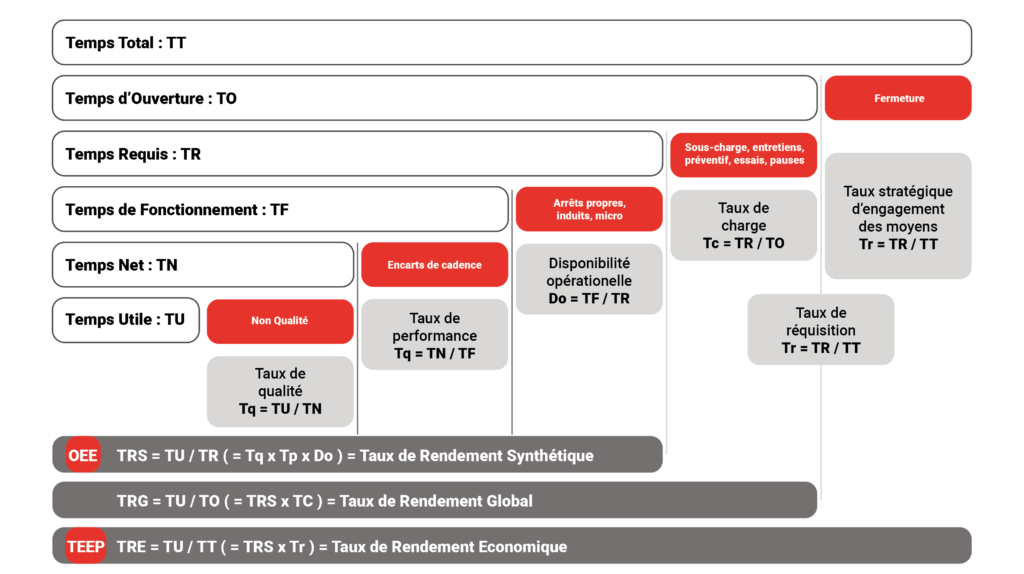
Le TRS vous présente une image précise de l’efficacité de votre processus de fabrication et rend facile le suivi des améliorations au fil du temps.
- Le Taux de rendement Général – TRG et le Taux de Rendement Economique – TRE
Le Taux de Rendement Général (TRG) et le Taux de Rendement Economique (TRE) sont moins souvent utilisés mais pourtant tout aussi intéressants dans une analyse pertinente de la productivité.
Le TRE offre une visibilité sur la rentabilité de votre machine par rapport à son temps d’utilisation sur une période précise. Il s’agit du temps réellement consacré à produire de la qualité sur 24 heures.
Ce taux fourni également des informations importantes sur la capacité globale d’une machine à délivrer une production de qualité, cela permet d’affiner la stratégie d’investissement de l’entreprise.
TRE = TU / TT
Le Taux de Rendement Général (TRG) permet de mesurer le niveau de rendement d’un équipement par rapport au temps d’ouverture réel de l’atelier, il s’agit donc du temps utilisé pour produire de la qualité sur la période d’ouverture de l’atelier.
Ce taux peut être révélateur en découvrant qu’il est nécessaire d’ajouter une équipe supplémentaire pour atteindre les objectifs de production attendus.
TRG = TU/TO
- Coût de temps d’arrêt (True Downtime Cost – TDC) et pourcentage du temps d’arrêt
Combien d’argent votre entreprise perd-elle à chaque minute ou heure lorsque vos machines sont en panne ? Voici la question fréquemment posée lors de l’analyse des pertes de production d’une machine mais qui malheureusement se pose seulement lorsque la machine tombe en panne.
Il faut savoir que même un faible pourcentage de diminution des temps d’arrêt peut sauver des millions de d’euros à l’entreprise. Par conséquent, en calculant votre coût de temps d’arrêt et en identifiant les améliorations associées, vous pouvez démontrer des gains de temps et d’argent, ainsi que des réductions des gaspillages.
- L’utilisation de la capacité
Le coût effectif de la possession et de l’entretien de l’équipement est diminué lorsque cet équipement est utilisé à pleine capacité. En mesurant la production qui est réellement produite par votre équipement et en la comparant à ce qui pourrait être produit, vous comprenez l’efficacité de votre opération.
Lorsque votre usine augmente son taux d’utilisation de la capacité, elle augmente son efficacité.
TEEPTRAK vous permet de détecter l’état de marche ou d’arrêt de chaque équipement, cette détection vous assurera un calcul automatisé de la majorité des indicateurs cités plus haut. De plus cela vous apportera un support non négligeable sur une retour direct de l’influence de vos actions d’amélioration sur vos machines et donc une meilleure visibilité du suivi de votre démarche Lean.
0 commentaires