GUIDE COMPLET
Qu’est ce que le TRS
(Taux de Rendement Synthétique) ?
Définition, méthode de calcul et conseils
Introduction au taux de rendement synthétique (TRS)
Qu’est-ce que le TRS ?
Le TRS (Taux de Rendement Synthétique), également connu sous l’acronyme anglais OEE (Overall Equipment Effectiveness), est un indicateur de performance qui a été développé par Seiichi Nakajima dans les années 1960. Il est conçu pour mesurer l’efficacité avec laquelle une installation industrielle est utilisée. Aujourd’hui, le TRS est l’indicateur le plus couramment utilisé pour évaluer la performance des équipements industriels.
Bien qu’il n’existe pas de consensus international sur cet indicateur, il est essentiel pour identifier les opportunités d’amélioration dans le processus de fabrication.
L’amélioration du TRS est généralement mesurée par rapport à une référence spécifique à chaque équipement, ce qui signifie que sa valeur n’est pas directement comparable entre différents types d’équipements ou différents sites de production. Maximiser le TRS, ou le TEEP (Total Effective Equipment Performance), ne garantit donc pas nécessairement l’optimisation globale de l’entité de production.
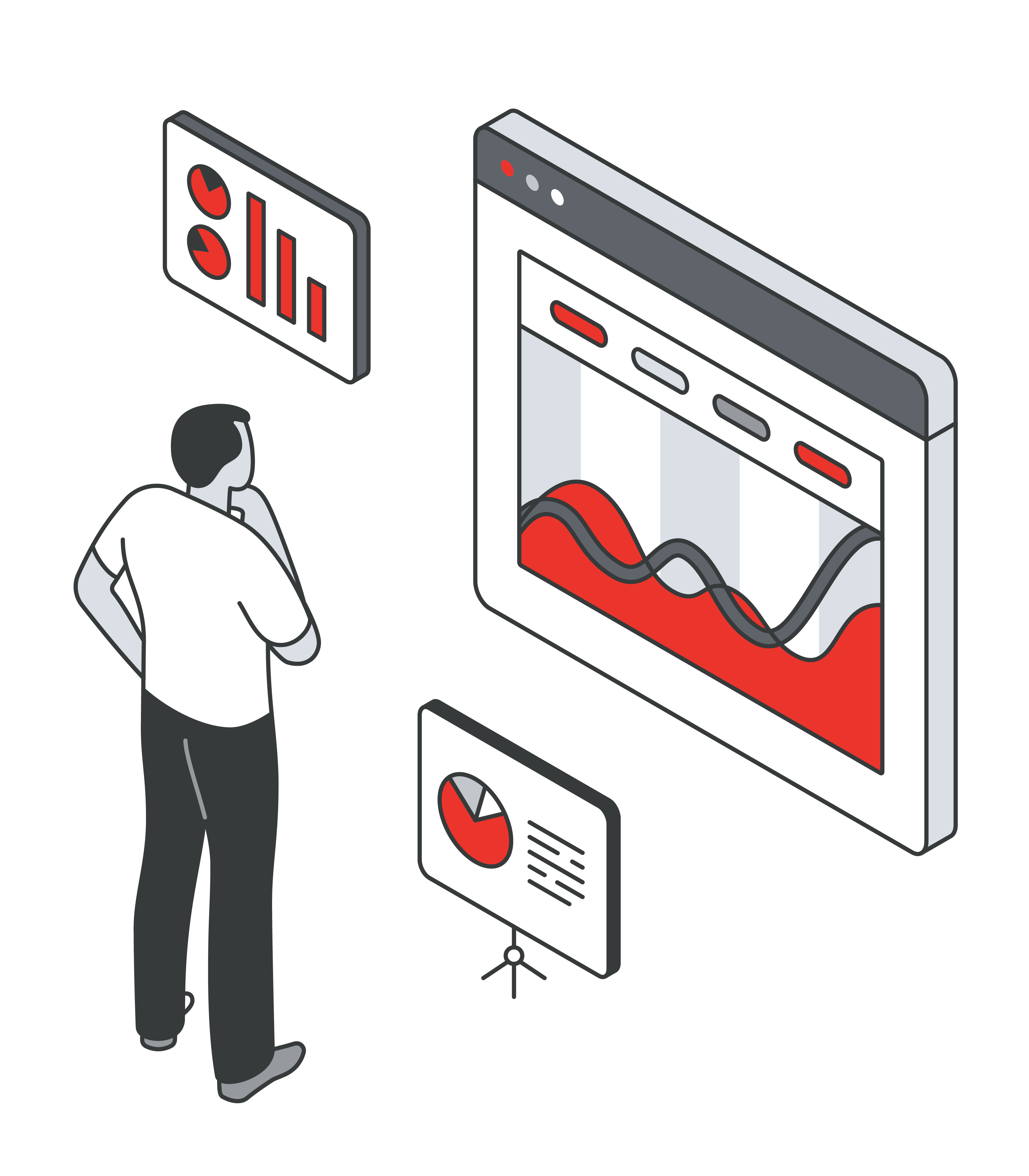
BASE
Calcul du TRS :
méthodologie et formules

Le calcul du TRS (Taux de Rendemant Synthétique) repose sur trois composants principaux :
1
Disponibilité
Il s’agit du pourcentage de temps pendant lequel l’équipement est disponible pour la production. On peut le calculer en divisant le temps de fonctionnement réel par le temps total prévu, puis en multipliant le résultat par 100.
2
PERFORMANCE
Cela mesure l’efficacité de l’équipement par rapport à sa capacité maximale. Il est généralement calculé en divisant la production réelle par la production théorique maximale, puis en multipliant le résultat par 100.
3
Qualité
Il s’agit du pourcentage de produits conformes aux spécifications de qualité. On peut le calculer en divisant le nombre de produits conformes par le nombre total de produits produits, puis en multipliant le résultat par 100.
4
TRS GLOBAL
Le TRS global est une mesure composite qui combine les trois facteurs mentionnés ci-dessus (disponibilité, performance et qualité) pour donner une indication globale de la performance de l’équipement.
1
Disponibilité
Il s’agit du pourcentage de temps pendant lequel l’équipement est disponible pour la production. On peut le calculer en divisant le temps de fonctionnement réel par le temps total prévu, puis en multipliant le résultat par 100.
2
PERFORMANCE
Cela mesure l’efficacité de l’équipement par rapport à sa capacité maximale. Il est généralement calculé en divisant la production réelle par la production théorique maximale, puis en multipliant le résultat par 100.
3
Qualité
Il s’agit du pourcentage de produits conformes aux spécifications de qualité. On peut le calculer en divisant le nombre de produits conformes par le nombre total de produits produits, puis en multipliant le résultat par 100.
4
TRS GLOBAL
Le TRS global est une mesure composite qui combine les trois facteurs mentionnés ci-dessus (disponibilité, performance et qualité) pour donner une indication globale de la performance de l’équipement.
TRS VS TRE VS TRG
Différence entre TRS
et autres indicateurs

TRS vs TRG : Quelles différences ?
Le TRS (Taux de Rendement Synthétique) et le TRG (Taux de Rendement Global) sont deux indicateurs souvent utilisés pour mesurer la performance des équipements industriels, mais ils se concentrent sur des aspects légèrement différents :
• Le TRS mesure l’efficacité globale des équipements en prenant en compte la disponibilité, la performance et la qualité, comme expliqué précédemment.
• Le TRG, en revanche, inclut également les pertes liées aux changements de série et les ajustements, offrant ainsi une vue plus étendue des pertes de production.
Ces différences font que le TRG peut souvent apparaître comme un indicateur plus sévère que le TRS, car il intègre plus de facteurs pouvant affecter négativement la performance.
Importance du TRS par rapport à d’autres métriques
Le TRS est crucial car il fournit une mesure directe de l’efficacité des équipements et une base solide pour l’amélioration continue. En comparaison avec d’autres métriques qui peuvent se concentrer sur des aspects isolés de la production, le TRS offre une perspective globale sur trois composantes clés qui sont essentielles pour toute entreprise cherchant à optimiser ses processus de fabrication et réduire ses coûts.
GUIDE
Mise en place
et suivi du TRS

Comment mettre en place un système de suivi du TRS ?
Mettre en place un système de suivi efficace pour le TRS implique plusieurs étapes clés :
- Définition des paramètres de mesure : Il est essentiel de définir précisément ce qui sera mesuré et comment, en s’assurant que les données recueillies seront fiables et pertinentes.
- Choix des outils de suivi : Utiliser des systèmes automatisés comme un système MES (Manufacturing Execution System) peut grandement faciliter la collecte et l’analyse des données.
- Formation et implication des équipes : Les opérateurs doivent être formés pour comprendre l’importance du TRS et comment leurs actions influencent directement les résultats.
Utilisation du système MES pour optimiser le TRS
Un système MES aide à collecter automatiquement les données nécessaires au calcul du TRS, en fournissant des informations en temps réel qui permettent de réagir rapidement pour rectifier les inefficacités. Ce type de système intègre souvent des fonctionnalités avancées de reporting et d’analyse, ce qui permet une surveillance constante et une amélioration continue des processus de production.
OUTILS
Indicateurs et causes
de perte de performance

Introduction aux solutions TEEPTRAK
TEEPTRAK est une solution technologique qui permet de suivre et d’analyser les performances des équipements en temps réel. Elle offre plusieurs outils spécifiques :
PerfTrak : pour suivre la performance des machines.
QualTrak : pour surveiller la qualité des produits.
PaceTrak : pour mesurer la cadence de production.
Chaque outil permet aux opérateurs de saisir les causes de déviation directement via une tablette, facilitant ainsi l’identification rapide des problèmes et l’adaptation des processus.
Construction des indicateurs de performance
Les données recueillies par les solutions TEEPTRAK sont utilisées pour construire des indicateurs de performance robustes. Ces indicateurs aident à comprendre les principales causes de perte de performance et à mettre en œuvre des actions correctives ciblées.
Nomenclature des pertes de performance pour OEE/TEEP
Pour le suivi efficace du TRS, certaines catégories de pertes telles que les « arrêts du site de production » et les « temps d’arrêt planifiés » ne sont généralement pas incluses dans le calcul du TRS, permettant de focaliser sur les pertes évitables et de maximiser l’efficacité opérationnelle.
optimisation
Amélioration du TRS :
stratégie et techniques

Utiliser la TPM pour améliorer le TRS
La Maintenance Productive Totale (TPM) est une approche proactive qui vise à maximiser l’efficacité des équipements industriels. La TPM implique tous les employés, des opérateurs de production aux responsables de maintenance, dans un effort collectif pour réduire les pertes et améliorer la performance des machines. En intégrant la TPM dans la stratégie d’entreprise, les organisations peuvent réaliser les avantages suivants pour améliorer leur TRS :
• Réduction des arrêts non planifiés : La maintenance préventive permet de détecter et de résoudre les problèmes avant qu’ils ne causent des arrêts de production.
• Amélioration de la qualité des produits : En maintenant l’équipement en parfait état, la TPM contribue à la production de pièces de haute qualité, réduisant ainsi le taux de rebuts.
• Augmentation de la productivité : Une machine bien entretenue fonctionne à sa capacité optimale, ce qui augmente la performance globale.
Méthode SMED et TRS
La Méthode SMED (Single-Minute Exchange of Die) est une technique qui vise à réduire le temps nécessaire pour les changements de format ou de configuration des équipements. Le SMED joue un rôle crucial dans l’amélioration du TRS, surtout dans les environnements de production qui nécessitent de fréquents changements de production. Les principaux bénéfices de l’application de la méthode SMED incluent :
• Diminution des temps d’arrêt : En réduisant les temps de changement, les périodes d’arrêt sont minimisées, ce qui augmente la disponibilité des machines.
• Flexibilité accrue : Avec des changements plus rapides, il est possible de répondre plus efficacement à la demande fluctuante et de produire de petites séries de manière économique.
• Meilleure utilisation des ressources : En optimisant les processus de changement, moins de temps et de ressources sont consacrés à des activités non productives.
Intégration de l’industrie 4.0 pour un TRS optimisé
L’industrie 4.0 représente la nouvelle vague de transformation numérique dans le secteur manufacturier. L’intégration de technologies avancées telles que l’Internet des Objets (IoT), l’intelligence artificielle (IA), et les systèmes cyber-physiques peut transformer significativement le calcul et l’amélioration du TRS. Voici comment l’industrie 4.0 peut contribuer à un TRS optimisé :
• Surveillance en temps réel : Les capteurs et les dispositifs IoT permettent de surveiller les conditions de fonctionnement des machines en temps réel, facilitant une maintenance prédictive précise et réduisant les arrêts imprévus.
• Analyse de données avancée : Avec l’IA et l’analyse de grandes quantités de données, il est possible d’identifier les tendances de défaillance et d’optimiser les processus de production pour améliorer le TRS.
• Automatisation accrue : Les robots et les systèmes automatisés peuvent prendre en charge des tâches répétitives ou dangereuses, augmentant ainsi la performance et la qualité tout en réduisant la fatigue humaine.
Vous souhaitez en découvrir plus sur le TRS ?
TRS & TRE
Études de cas
et analyses récentes

Analyse de cas : Impact de l’amélioration du TRS
L’impact de l’amélioration du TRS peut être illustré par plusieurs études de cas dans divers secteurs industriels. Voici quelques exemples concrets :
Industrie automobile : Une usine de fabrication de composants automobiles a mis en œuvre un programme de TPM pour améliorer son TRS. Après un an, l’usine a vu son TRS augmenter de 65% à 85%. Cette amélioration a entraîné une réduction significative des temps d’arrêt et une augmentation de la production sans nécessiter d’investissements supplémentaires en équipements.
Fabrication de dispositifs médicaux : Par l’application de la méthode SMED, une entreprise spécialisée dans les dispositifs médicaux a réduit le temps de changement de ses équipements de 50 minutes à 15 minutes, augmentant ainsi la disponibilité des machines et améliorant le TRS de 72% à 90%. Cette amélioration a également contribué à une meilleure réponse aux demandes du marché en termes de variété de produits.
Secteur des boissons : L’introduction de technologies de l’Industrie 4.0 dans une brasserie a permis de surveiller en temps réel les performances des équipements, aboutissant à une amélioration du TRS de 10 points. Les données collectées via des capteurs intelligents ont aidé à optimiser les processus et à réduire les pertes de qualité.
Ces exemples montrent que des initiatives ciblées sur l’amélioration du TRS peuvent avoir des retombées positives directes sur la capacité de production et la rentabilité des entreprises.
Données récentes : Tendances et innovations
Les tendances actuelles et les innovations en matière de TRS incluent :
Digitalisation accrue : L’utilisation de plateformes numériques pour le suivi et l’analyse du TRS est en hausse. Ces outils permettent de collecter et d’analyser des données de production en temps réel, facilitant des décisions plus rapides et plus précises.
Maintenance prédictive : Avec les avancées en IA et en analyse de données, la maintenance prédictive devient une pratique courante pour prévenir les défaillances avant qu’elles ne surviennent, contribuant ainsi à l’amélioration du TRS.
Personnalisation des solutions de suivi : Les solutions de suivi du TRS deviennent de plus en plus personnalisables, permettant aux entreprises de s’adapter précisément à leurs besoins spécifiques et d’intégrer le TRS dans des systèmes de gestion de production plus larges.
Ces innovations suggèrent une évolution continue de la gestion de la performance des équipements, où le TRS joue un rôle central pour aider les entreprises à rester compétitives dans un environnement industriel en rapide mutation.
TRS & TRE
Conclusion
Points clés et Conseils

Synthèse des points clés
Le Taux de Rendement Synthétique, ou TRS, est un indicateur fondamental pour mesurer et optimiser la performance des équipements industriels. À travers son calcul, qui intègre les dimensions de disponibilité, performance et qualité, le TRS offre une vue d’ensemble précise de l’efficacité de la production. Les méthodes pour améliorer le TRS, telles que la TPM, la méthode SMED, et l’intégration de l’Industrie 4.0, montrent des résultats concrets en augmentant la productivité et en réduisant les coûts.
Conseils pratiques pour les responsables de production
Pour les responsables de production, ingénieurs qualité et consultants en performance industrielle, l’application rigoureuse et systématique des principes du TRS est essentielle. Il est recommandé de mettre en place un système de suivi continu, d’utiliser des outils de mesure modernes comme les systèmes MES, et de rester informé des dernières innovations technologiques qui peuvent aider à pousser l’efficacité des équipements à leur maximum. L’objectif est de transformer les données en actions concrètes qui génèrent une amélioration continue de la production.
En conclusion, le TRS n’est pas juste un chiffre à atteindre, mais une démarche continue vers l’excellence opérationnelle. En se concentrant sur les améliorations mesurables et en adoptant des technologies avancées, les entreprises peuvent réaliser des gains significatifs en termes de performance, de qualité et de satisfaction client.