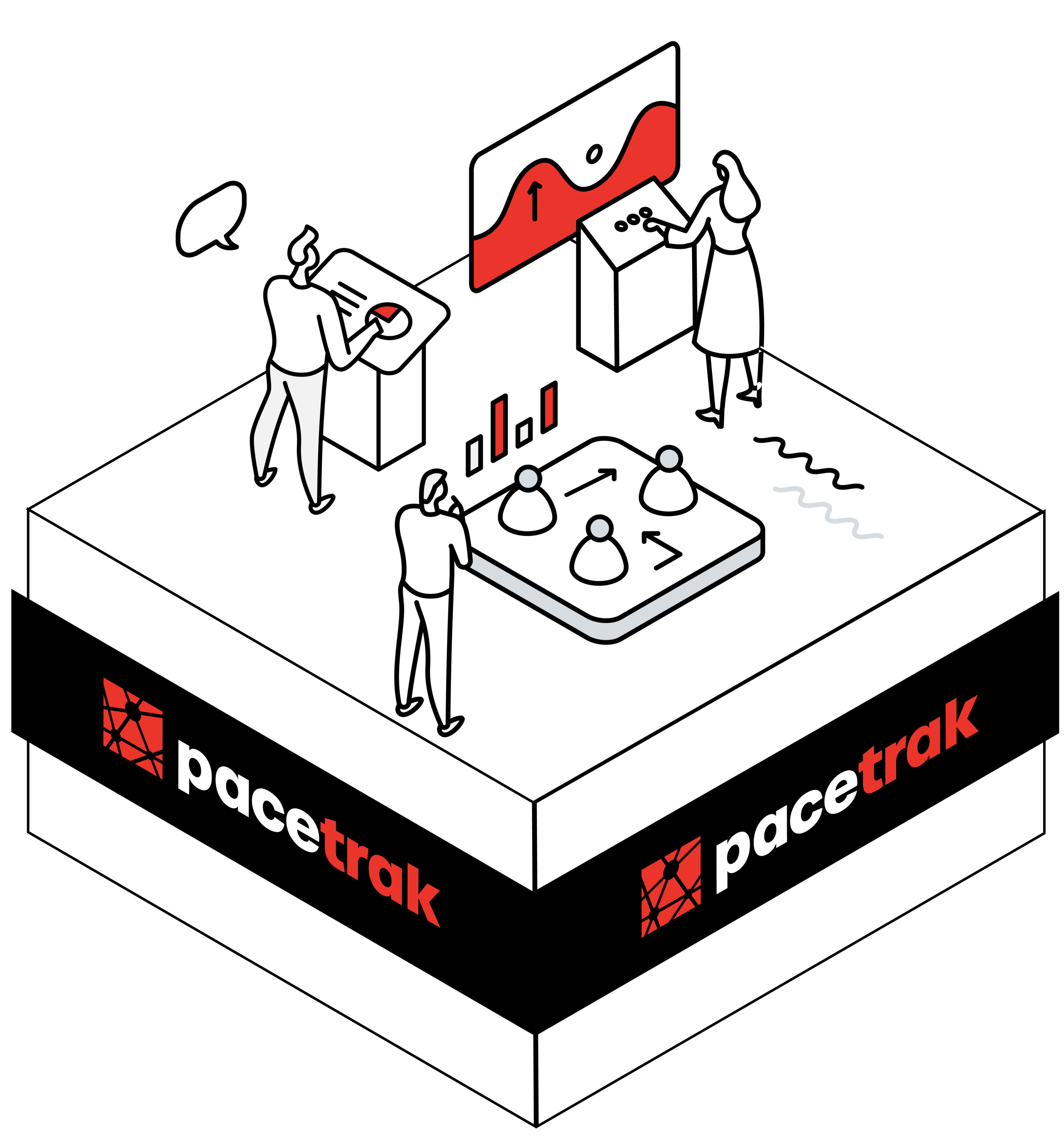

the optimised solution for monitoring the performance of manual tasks
PACETRAK
Efficiently control the pace of your operations
Pacetrak is an optimized solution for tracking the performance of manual tasks, specially designed to give field teams clear, precise visibility of opportunities to improve their missions.
By quickly identifying bottlenecks in the execution of tasks, PaceTrak helps optimize productivity and streamline routing times. What’s more, by improving operators’ working conditions, our solution contributes to their motivation and satisfaction, creating a more harmonious and efficient work environment.
Choose PaceTrak and transform your operations into a model of optimum performance.
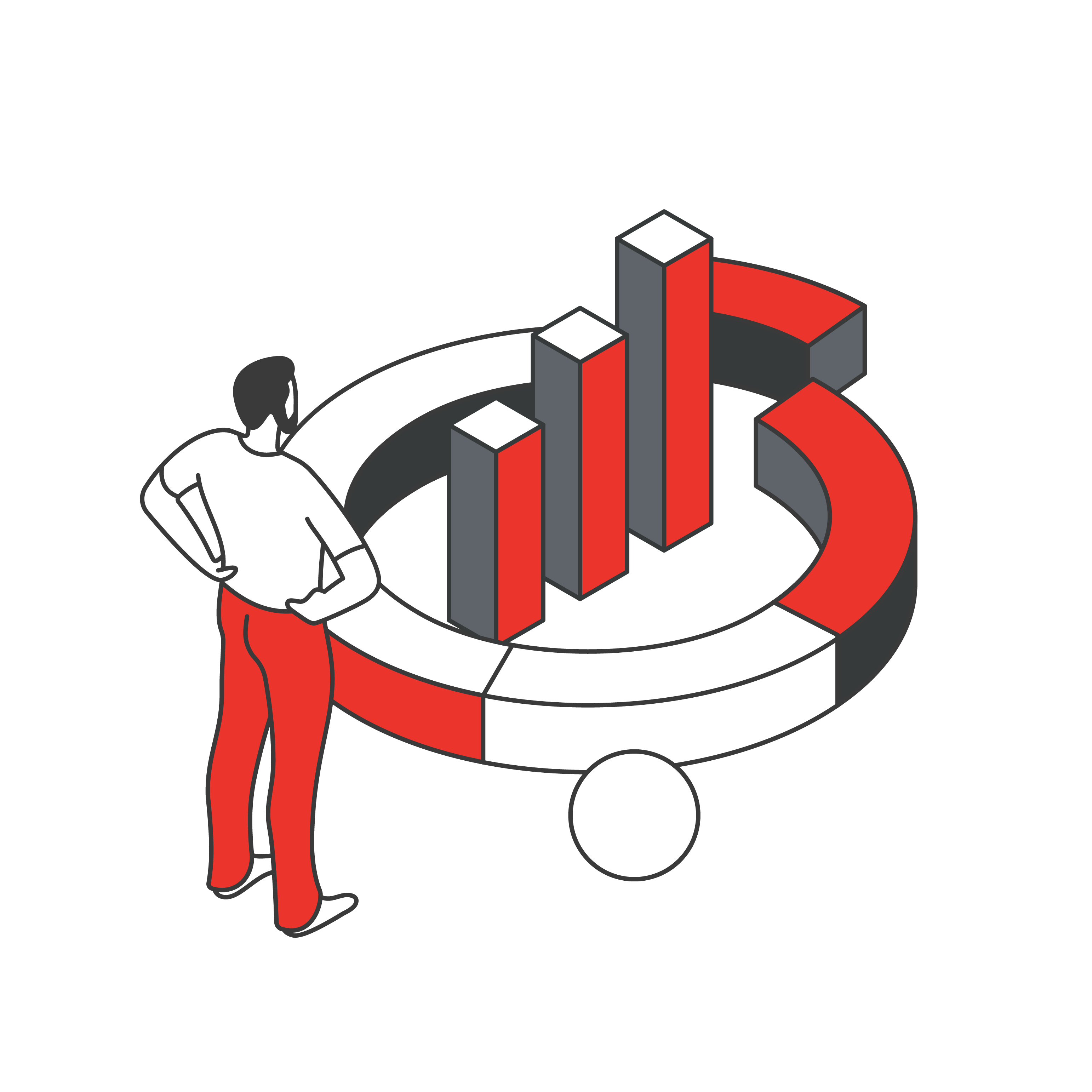
Operating principle
The PaceTrak solution is designed to be both simple and effective. By configuring a standard time and a list of potential causes of lost time, the application can capture a signal for each part produced or each stage reached in your production process. This can be done via a variety of devices, such as the tablet’s touch screen, a button, a foot pedal or a strategically placed sensor.
When PaceTrak automatically detects a time loss, the person responsible is immediately alerted so that they can identify the reason. This process gathers valuable information, making it easier to analyse and understand the causes of time discrepancies.
With PaceTrak, you can quickly identify and correct inefficiencies, optimising your production.
Functionalityㅤ
PaceTrak enables users to detail precisely the causes of non-performance, making this tool an essential asset for the continuous improvement of operations. Incidents can be quickly reported and analysed to optimise production processes.
PaceTrak also incorporates all the functions you need to optimise your workstation: it allows you to fill in forms (ideal for preventive maintenance) and quality reports, and effectively manage rejects by identifying defective products and recording the causes of rejection.
It also makes it easier to track break times and provides easy access to workstation files, simplifying reference processes and access to the necessary information.
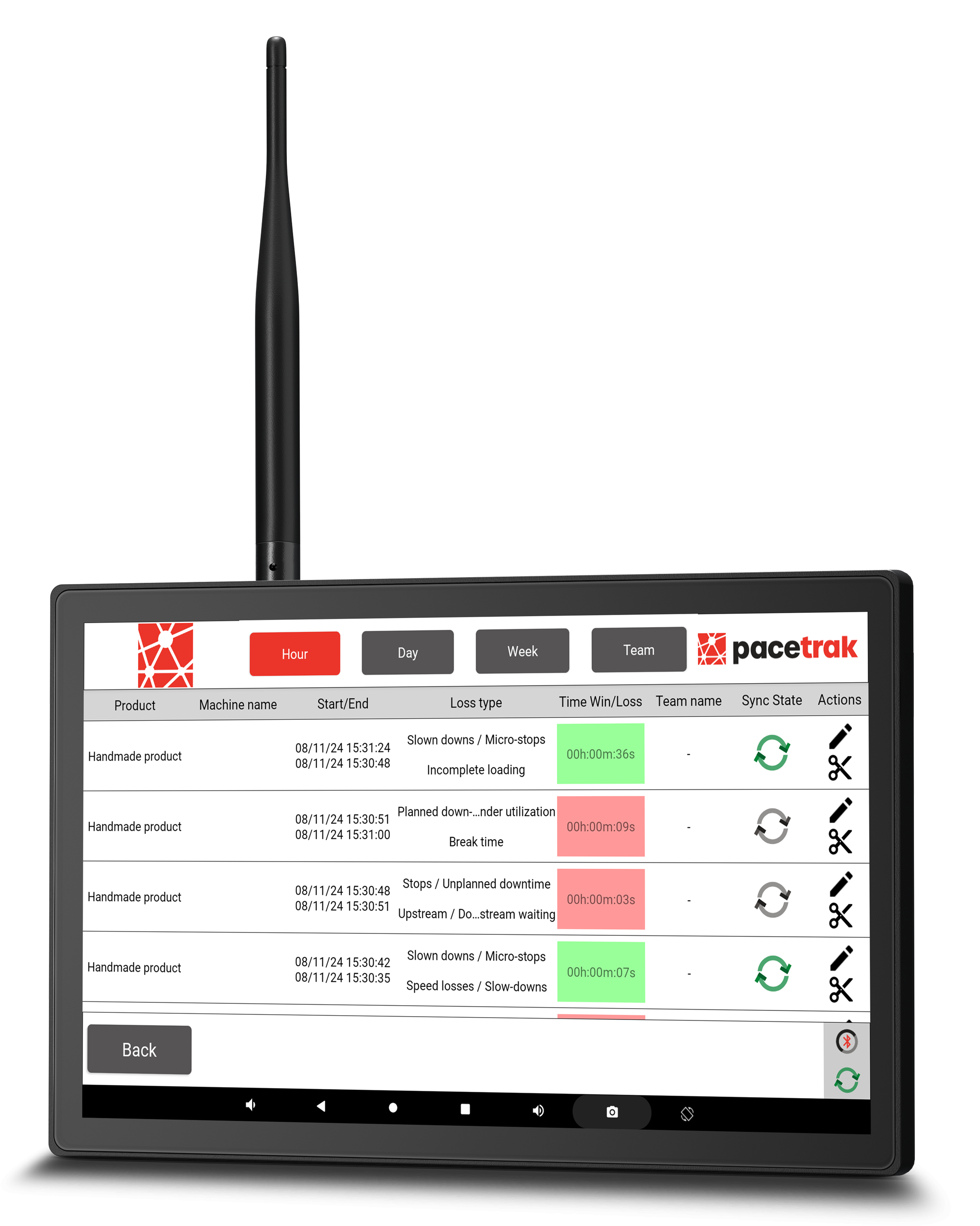
INTUITIVE
The tablet interface

An interface dedicated to monitoring the performance of manual tasks.
PaceTrak’s tablet interface enables operators to instantly qualify deviations from standards, while remaining at their workstations. Designed specifically for the field, this ergonomic interface ensures fast, intuitive use.
Thanks to its well-thought-out design, the interface minimizes interruptions by enabling fluid navigation and rapid data entry. Operators can easily record anomalies and deviations, enabling an immediate and effective response to problems. Touch functionality ensures high responsiveness, even in demanding work environments.
In addition, the tablet interface provides direct access to essential information, such as work instructions, safety protocols and technical specifications. This simplifies reference processes and ensures that operators always have the data they need to make informed decisions, contributing to continuous improvement and increased productivity.
QUICK AND EASY
Installation stages

Pacetrak is available in automatic and manual versions. With or without an acquisition module.
In manual mode, the operator declares the start and end of his range or tasks.
In automatic mode, the start and end of a task are retrieved automatically.
1 • Install the tablet at the workstation
2 • Connect the module to a signal (optional)
3 • Enter your ranges and associated times
4 • Configure your causes of loss
5 • Gain efficiency!
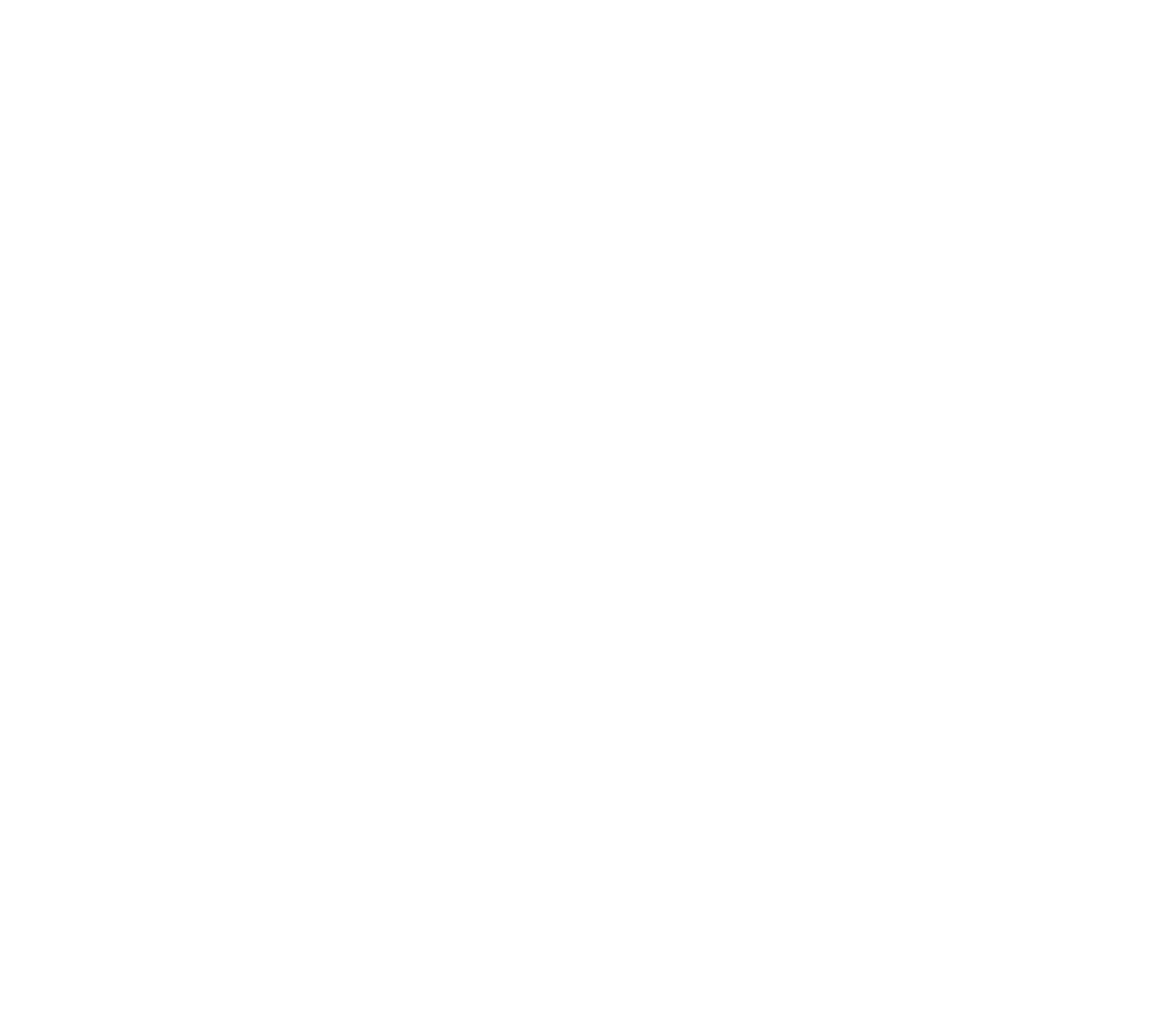
PACETRAK
Supervision site

Data analysis
Take advantage of powerful analysis tools to examine data by the time period and scope of your choice, whether it’s a machine, a workshop, a production line, a plant or a team. Tailor your analyses to obtain relevant, detailed information.
The PaceTrak supervision site is your essential tool for optimised, proactive production management. With its robust, customisable features, it enables you to turn data into action, improving the performance and profitability of your industrial operations. Explore now how our monitoring site can revolutionise the way you work.
Analysis tools
Access a comprehensive range of analysis tools, including performance indicators, real-time alarms, historical data, Pareto analysis of downtime, automatic count reports and scrap rate display. These features help you to monitor, evaluate and optimise your production processes on an ongoing basis.
Smartphone alarms
Receive instant alerts on your smartphone in the event of performance deviations or machine stoppages. Stay informed and responsive wherever you are, to minimise interruptions and maximise production efficiency.
Access to raw data
Extract raw data from your system to carry out in-depth customised analyses. This functionality allows you to manipulate and exploit information according to your specific needs, making it easier to take strategic decisions.
Manual entry of values
Use interactive forms to view and monitor self-checks. Configure periodic statements according to the frequency, quantity and type of action required (e.g. temperature, weight). Ensure the compliance and quality of your operations through regular, rigorous checks.
Data analysis
Take advantage of powerful analysis tools to examine data by the time period and scope of your choice, whether it’s a machine, a workshop, a production line, a plant or a team. Tailor your analyses to obtain relevant, detailed information.
Analysis tools
Access a comprehensive range of analysis tools, including performance indicators, real-time alarms, historical data, Pareto analysis of downtime, automatic count reports and scrap rate display. These features help you to monitor, evaluate and optimise your production processes on an ongoing basis.
Access to raw data
Extract raw data from your system to carry out in-depth customised analyses. This functionality allows you to manipulate and exploit information according to your specific needs, making it easier to take strategic decisions.
Smartphone alarms
Receive instant alerts on your smartphone in the event of performance deviations or machine stoppages. Stay informed and responsive wherever you are, to minimise interruptions and maximise production efficiency.
Manual entry of values
Use interactive forms to view and monitor self-checks. Configure periodic statements according to the frequency, quantity and type of action required (e.g. temperature, weight). Ensure the compliance and quality of your operations through regular, rigorous checks.
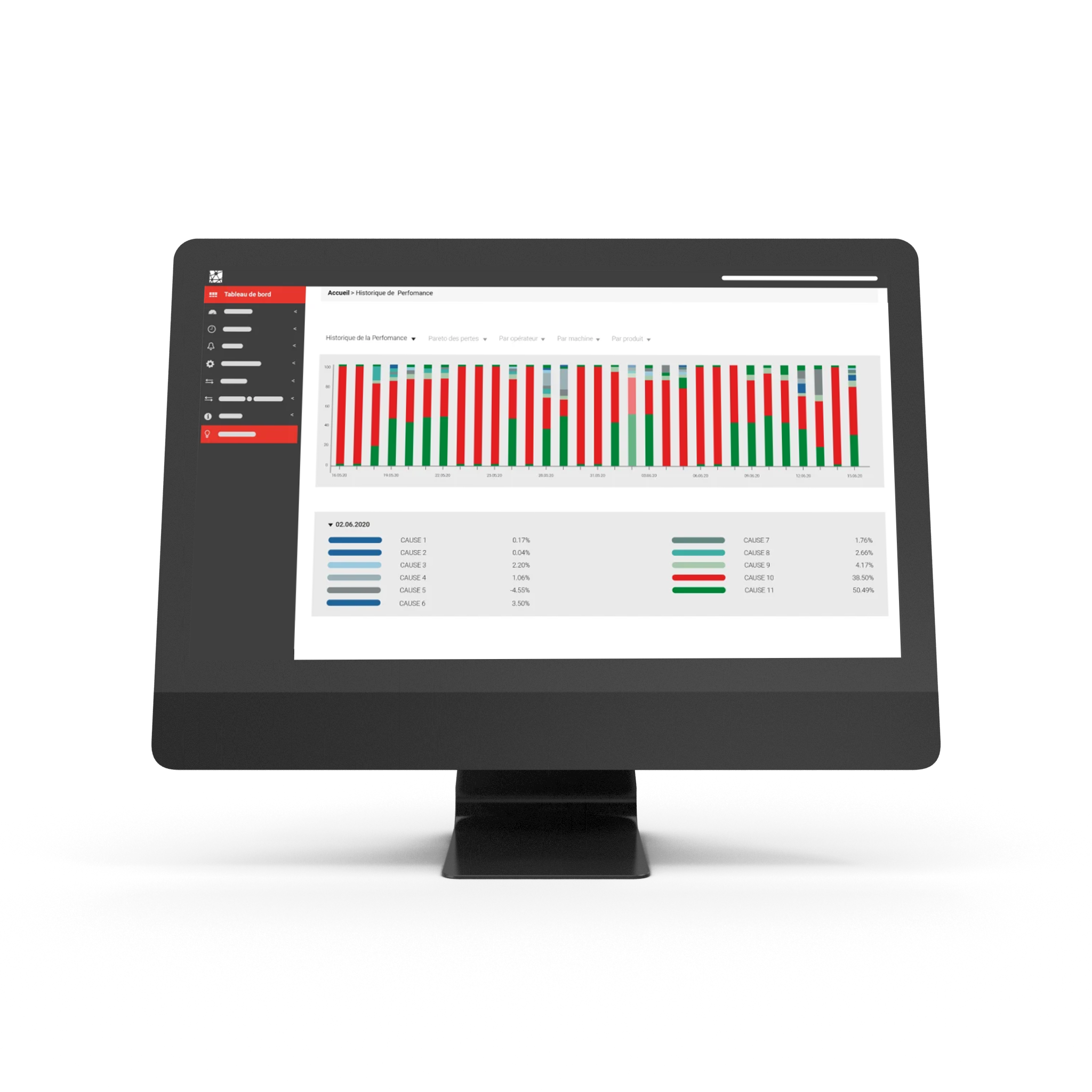
SPECIFICATIONS
The different versions of PaceTrak
Choose the PaceTrak
that meets your needs
PaceTrak Small and Medium Series
Ideal for medium- and small-scale production, PaceTrak Medium/Small runs offers exceptional flexibility. It allows rapid adaptation to production changes and variations in demand. The system ensures accurate, detailed management of every stage of production, helping to maintain quality and minimise wasted time. Its customisation capabilities allow you to configure the system to your specific needs, ensuring optimum operational efficiency.
PaceTrak Large Series
Optimised for large-scale production, PaceTrak Large Series is designed to handle high volumes with maximum efficiency. The system provides rigorous monitoring of every part produced, enabling rapid detection of deviations and immediate correction of problems. With its advanced reporting and analysis capabilities, you can easily identify trends and optimise processes to increase productivity and reduce costs.
PaceTrak Complex Ranges
Designed for production involving complex processes, PaceTrak Complex Routings is perfect for manufacturing environments requiring high accuracy and detailed tracking. The system provides advanced routing management, allowing each step to be monitored with attention to detail. It makes it easy to identify critical points and bottlenecks, enabling targeted interventions to improve production flow and ensure high-quality results. Its in-depth analysis tools help to understand and optimise complex processes, making your production more agile and efficient.