How do you carry out a Lean diagnosis? All you need to know in 4 key steps

If your company’s Lean approach is to be a success and sustainable, you need to structure your project, and to do this, a Lean diagnosis is an essential tool.
Carrying out a Lean diagnosis will enable you to analyse and share the initial state of your performance, identify potential improvements and target your objectives.
Why carry out a diagnostic?
Imagine yourself in the context of a medical consultation: the doctor is trying to understand your condition, so his research will be based on auscultation and listening to the patient, then supplemented by targeted analyses. Without following this process, your doctor will be unable to know what ails you. Carrying out a diagnosis within your organisation to initiate your Lean approach follows the same logic as the example given above.
There can be many reasons for carrying out a diagnosis, and here is a non-exhaustive list:
-
-
- Customer needs not met
- Your sector of activity requires you to evolve and adapt rapidly
- Your performance is poor
- Growth and/or acquisitions cause malfunctions
- Deterioration in internal and customer communications
- Observation of backtracking on actions put in place
- No guidelines for managing your priorities
- No involvement
- …
-
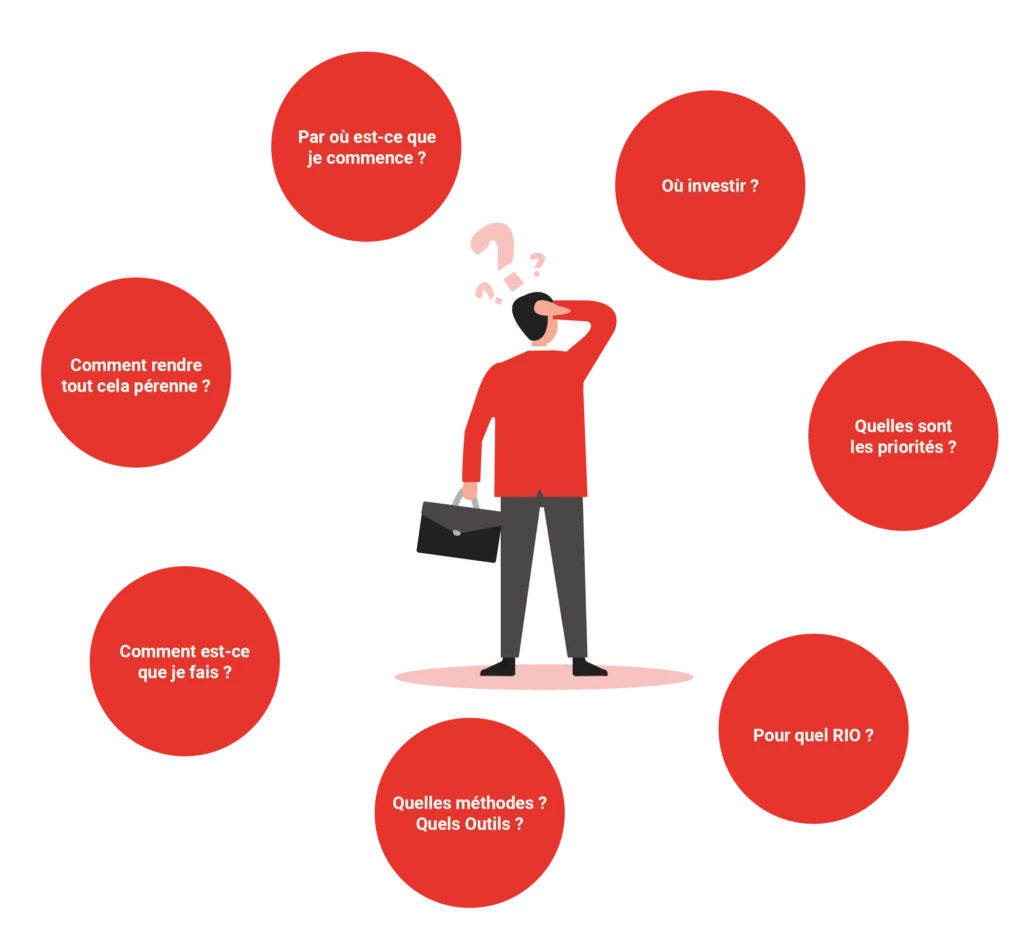
Principle of the approach
The Lean diagnosis is a prerequisite for your Lean approach. It is an initial inventory based on figures, interviews and observations. It provides a basis on which to work and decide on priority actions, then proposes a roadmap over several months.
The results will then be shared with senior management, middle management and the field teams concerned.
It is a collaborative effort.
4 key stages in the diagnostic process
Preparing the Lean diagnosis: understanding the context and objectives, defining the scope, segmentation, people to be audited, timetable, making appointments. Diagnosis : This phase takes place in the field with operational managers and process pilots, through interviews and visits to completed or ongoing Lean projects. Data is collected. Drawing up the diagnosis : Draw up a summary of the company’s situation in each area of analysis. This summary is drawn up for each of the company’s predefined sectors. Roadmap presentation: Lean methods awareness, workstreams and planning. Definition of priority projects, management methods, resources, etc.
The TeepTrak solution, a diagnostic tool?
The TeepTrak solution fits in perfectly with the diagnosis stage, and will be a major ally in your data collection and analysis. Indeed, Lean projects on machines are frequent, thanks to TeepTrak, this diagnosis stage is simplified and the impact of improvement actions on your machine is automatically visible via the KPIs that can be collected with the TeepTrak solution.
0 Comments