What are the standards for measuring your OEE? We explain it all here

The synthetic rate of return (SRR) or Overall Equipment Effectiveness (OEE) is a performance indicator developed by Seiichi Nakajima in the 1960s to measure the utilisation rate of an industrial installation. TRS is the most frequently used indicator today for measuring equipment performance, even though there is currently no international consensus on this indicator.
However, the measurement provided by such an indicator is relative and is, in practice, used to identify areas for improvement. The improvement in OEE is measured against a benchmark for a given piece of equipment; the value of this indicator is therefore specific to that piece of equipment and is not comparable with other types of equipment in other departments or plants. Maximising OEE or TEEP does not necessarily mean achieving the global optimum for the production entity.
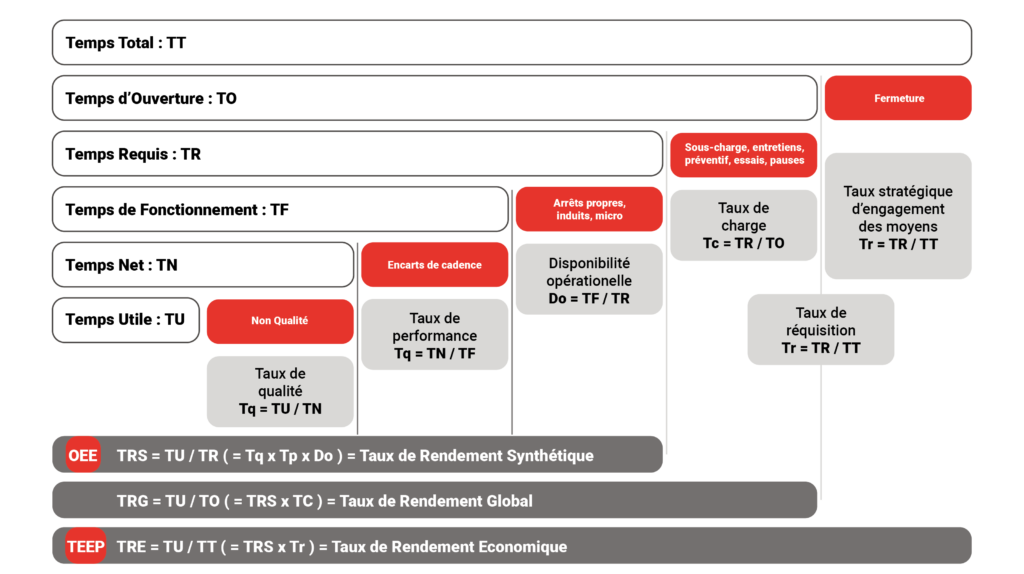
INDICATORS AND CAUSES OF LOSS OF PERFORMANCE
TeepTrak allows you to assign a set of fully configurable categories of causes of loss of performance to each piece of equipment or area monitored. With the PerfTrak, QualTrak and PaceTrak solutions, these causes can be entered by the operator on his tablet when a production deviation (machine stoppage, underperformance, etc.) is reported to him by the TEEPTRAK module.
These causes of loss will be attached to groups of causes which will make up the performance indicators. When constructing an indicator, certain groups of causes may be included or excluded from the calculation of the indicator.
Ci-dessous : un exemple de nomenclature de pertes de performance pour chaque catégorie type du calcul d’indicateurs OEE/TEEP. Pour suivre un OEE (TRS), les catégories « Arrêt du site de production » et « Temps d’arrêt planifié » ne seront pas prises en compte dans son calcul.
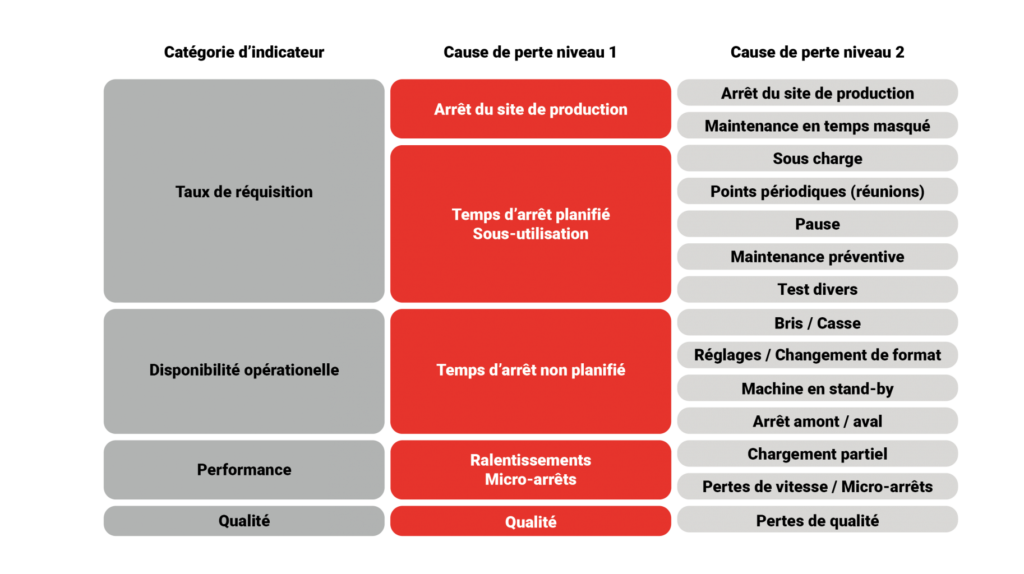
0 Comments